Plastic extrusion for detailed profiles and custom designs
Plastic extrusion for detailed profiles and custom designs
Blog Article
A Comprehensive Guide to the Process and Benefits of Plastic Extrusion
In the large world of manufacturing, plastic extrusion arises as a extremely effective and crucial process. Altering raw plastic into constant accounts, it provides to a plethora of industries with its exceptional convenience.
Understanding the Basics of Plastic Extrusion
While it might show up facility at initial look, the procedure of plastic extrusion is essentially straightforward. The procedure starts with the feeding of plastic material, in the form of powders, pellets, or granules, into a warmed barrel. The designed plastic is then cooled down, solidified, and cut right into preferred lengths, finishing the process.
The Technical Process of Plastic Extrusion Explained

Kinds of Plastic Suitable for Extrusion
The option of the right type of plastic is a vital facet of the extrusion process. Different plastics supply unique residential or commercial properties, making them a lot more suited to particular applications. Polyethylene, for instance, is commonly used because of its affordable and very easy formability. It supplies excellent resistance to chemicals and moisture, making it perfect for products like tubing and containers. Polypropylene is one more preferred choice due to its high melting point and resistance to exhaustion. For even more durable applications, polystyrene and PVC (polyvinyl chloride) are often chosen for their toughness and durability. These are usual alternatives, the option ultimately depends on the specific needs of the item being produced. So, understanding these plastic kinds can dramatically improve the extrusion process.
Contrasting Plastic Extrusion to Other Plastic Forming Approaches
Comprehending the kinds of plastic appropriate for extrusion leads the method for a wider conversation on just how plastic extrusion compares to various other plastic developing approaches. These include shot molding, impact molding, and thermoforming. Each technique has its one-of-a-kind uses and benefits. Shot molding, for example, is exceptional for developing elaborate components, while blow molding is ideal for hollow things like bottles. Thermoforming excels at developing superficial or huge parts. Plastic extrusion is unmatched when it comes to creating constant accounts, such as pipelines, gaskets, and seals. It likewise permits a consistent cross-section along the length of the product. Therefore, the selection of method mainly relies on the end-product demands and specs.
Secret Advantages of Plastic Extrusion in Manufacturing
In the realm of manufacturing, plastic extrusion offers many considerable benefits. One notable benefit is the cost-effectiveness of the procedure, that makes it an economically appealing production approach. In addition, this method offers exceptional product flexibility and enhanced manufacturing speed, consequently boosting general manufacturing efficiency.
Cost-Effective Manufacturing Technique
Plastic extrusion jumps to the leading edge as a cost-effective production technique in manufacturing. Furthermore, plastic extrusion requires much less energy than traditional manufacturing techniques, adding to reduced functional prices. Generally, the economic advantages make plastic extrusion a highly attractive option in the manufacturing industry.
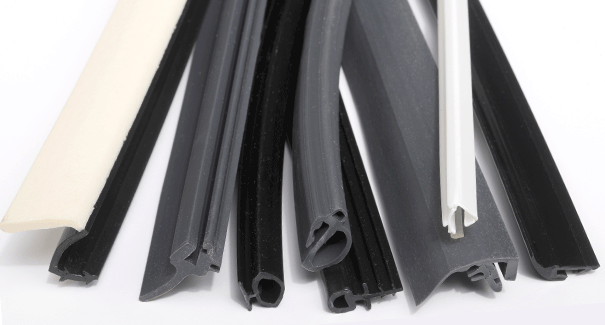
Superior Item Flexibility
Past the cost-effectiveness of plastic extrusion, one more considerable advantage in making lies in its exceptional product versatility. This makes plastic extrusion an ideal option for markets that call for customized plastic elements, such as automobile, building, and product packaging. In significance, plastic extrusion's product versatility fosters innovation while enhancing operational effectiveness.
Boosted Production Speed
A substantial advantage of plastic extrusion depends on its enhanced manufacturing speed. This production process permits high-volume production in a reasonably short time period. It can producing long, continual plastic accounts, which substantially reduces the manufacturing time. This high-speed manufacturing is specifically beneficial in sectors where large amounts of plastic components are more needed within limited deadlines. Couple of other production processes can match the rate of plastic extrusion. In addition, the ability to maintain regular high-speed manufacturing without giving up item top quality sets plastic extrusion in addition to various other techniques. The boosted manufacturing speed, therefore, not only enables suppliers to fulfill high-demand orders but additionally adds to enhanced efficiency and cost-effectiveness. This advantageous attribute of plastic extrusion has made it a recommended choice in many sectors.
Real-world Applications and Effects of Plastic Extrusion
In the realm of production, the strategy of plastic extrusion holds profound value. This procedure is extensively used in the manufacturing of a variety of items, such as plastic tubing, window structures, and weather stripping. Consequently, it greatly affects sectors like building, packaging, and automobile markets. Furthermore, its influence encompasses everyday items, from plastic bags to toothbrushes and non reusable cutlery. The financial advantage of plastic extrusion, mostly its cost-effective and high-volume output, has actually revolutionized production. Nevertheless, the environmental effect of plastic waste continues to be an issue. Therefore, the sector is persistently pursuing innovations in biodegradable and recyclable products, suggesting a future where the benefits of plastic extrusion can be maintained without jeopardizing ecological sustainability.
Final thought
To conclude, plastic extrusion is a extremely reliable and effective technique of transforming resources right into varied items. It offers countless benefits over various other plastic developing view approaches, including cost-effectiveness, high outcome, marginal waste, and style versatility. Its influence is exceptionally felt in different sectors such as construction, auto, and customer goods, making it a critical procedure in today's manufacturing landscape.
Delving much deeper into the technological process of plastic extrusion, it begins with the selection of the suitable plastic material. When cooled, the plastic is cut right into the required lengths or injury onto reels if the product is a plastic film or sheet - plastic extrusion. Comparing Plastic Extrusion to Other Plastic Forming Techniques
Comprehending the kinds of plastic ideal for extrusion leads the way for a broader conversation on exactly how plastic extrusion piles up versus various other plastic developing methods. Few other manufacturing my link procedures can match the rate of plastic extrusion.
Report this page